Delphi's innovative new engine mounts for Porsche GT3
Now entering production for a prestigious European supercar, the new mounts use computer-controlled fluid to absorb more engine vibrations and help control powertrain movement during rapid direction changes.
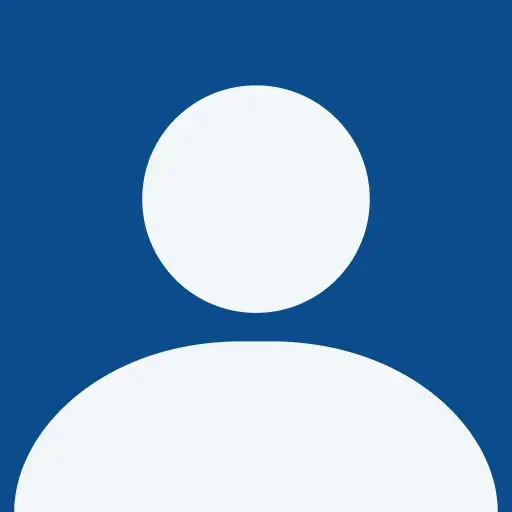
A ground-breaking new powertrain mount has been developed by Delphi Corporation. Using magneto rheological (MR) fluid that can change its dynamic rate in real time, the new MR Mount prevents the build-up of resonance in a system by maintaining control of the mounted mass across all appropriate frequencies.
As well as significantly reducing powertrain noise and vibration, the new mount can improve vehicle performance and stability and help isolate the occupants from torque step events such as those generated by start-stop operation.
"This is the first technology that allows precise real-time management of the relevant frequencies created by an automotive powertrain, including the challenging low frequencies and higher amplitudes caused by transient torque events," says Delphi's MR Mount manager Timothy Schlangen.
"Vehicle manufacturers working closely with Delphi have been excited by the wide range of benefits that MR Mounts can bring and by the increasing list of ways they can improve performance, safety and refinement through vehicle-specific tuning." The first application will be for engine mounts in the new (2010) Porsche GT3, helping to improve traction and stability for one of Europe's most outstanding driver's cars.
Powertrain mounts provide a wide range of functions. As well as suspending the mass of the engine and transmission, the mounts provide a reaction point for torque and isolate the body of the vehicle from powertrain noise and vibration. With conventional technology it is impossible to optimize the way the mounts behave for each function and each dynamic state.
The system uses magnetically soft iron particles suspended in a base fluid, held within a cavity in the rubber body of the mount. When a magnetic field is applied by a coil, the particles become aligned, increasing the sheer stress and therefore the resistance to flow. The stronger the magnetic field, the higher the dynamic rate (effectively the stiffness) of the system.
The current is controlled by a processor that receives data already available on the vehicle data bus. This data can include throttle position, road speed, engine speed, temperature and any other information required to deliver the level of control specified by the vehicle manufacturer. Closed loop feedback is provided by direct measurement of the fluid pressure in the system, ensuring real time compensation for changing conditions as the system components age.
Benefits include improvements in powertrain isolation, vehicle stability and traction. "The level of sound and vibration transfer can be greatly reduced," says Schlangen. "It also opens new opportunities for brand-specific tuning and vehicles whose character changes depending on the driver's requirement, perhaps linked to other active systems such as dampers and a sports exhaust to transform the noise and feel at the flick of a switch."
The system also provides a solution to the refinement and stability issues associated with torque transients created by events such as engine start (useful with stop-start systems), sudden wide open throttle, braking, gear changes and moving an automatic transmission into drive. It can also improve traction, stability and occupant comfort on rough roads by managing the low frequencies created by the movement of large powertrain masses. For hybrid vehicles, it provides an affordable damping system for the wide range of frequencies generated by two different power sources.
MR Mounts also bring manufacturing and logistics benefits because the same component can be electronically tuned for a wide range of applications, allowing the parts count to be reduced. Its ability to reduce powertrain-related noise and harshness also means that other systems for sound and vibration absorption can be simplified, further reducing weight and simplifying assembly.
In the GT3 application, Porsche is using the technology to improve traction and stability during hard acceleration and cornering. The control unit will stiffen the mount when torque is applied, reducing 'power hop' that can momentarily reduce the tyre contact patch. Stiffening will also reduce engine roll and maintain balanced torque transfer across the vehicle.
[IMG]http://www.oneshift.com/showroom/uploadimages/resized-2009071301609725.jpg[/IMG]
[IMG]http://www.oneshift.com/showroom/uploadimages/resized-2009071301536801.jpg[/IMG]
Credits: JRC
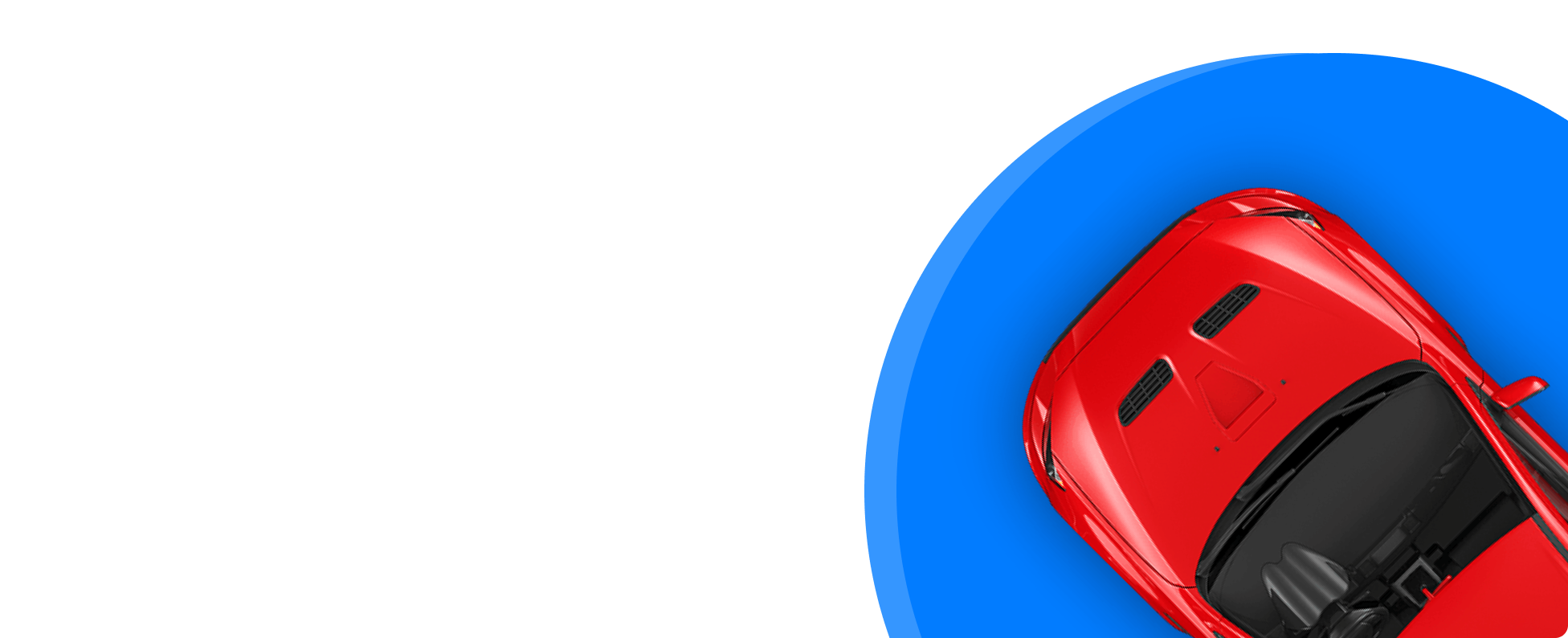
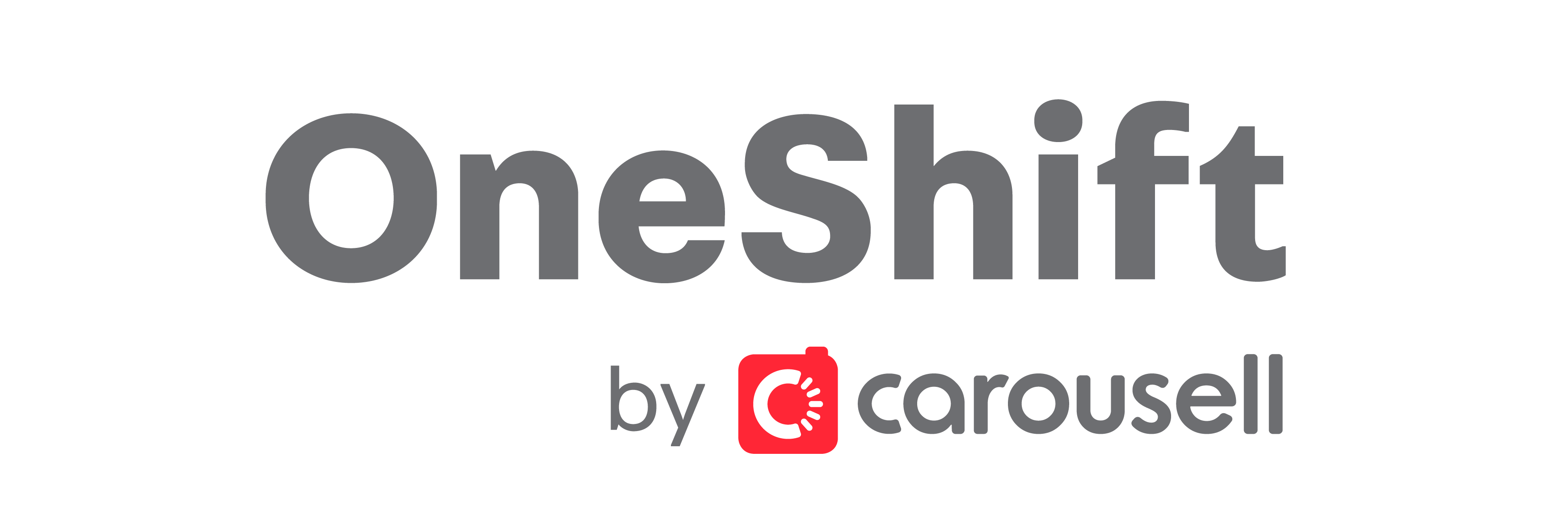
Get the Best Price for your used car
from 500+ dealers in 24 hours
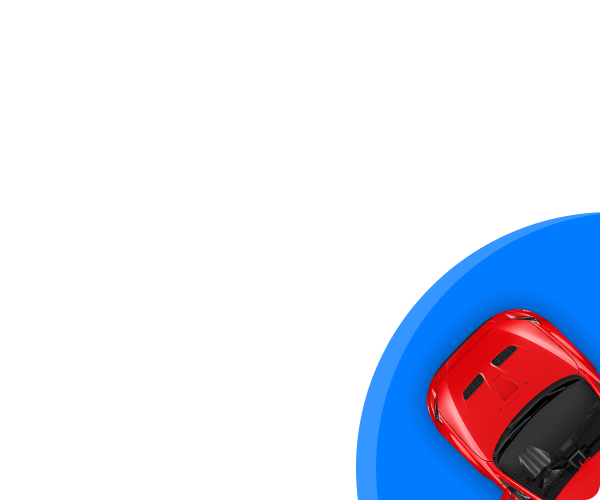
- Convenient and Hassle-Free
- Consumer Protection
Transparent Process
With No Obligation